Lubricant in use by physical and chemical effects, as well as the effects of pollution and decay occur, lubricant properties of changes is not well protected internal combustion engine, it needs to be replaced. (1) by heat and mechanical shear effects: evaporation of light components and theviscosity showed an increase in fuel consumption, mechanical shear viscosity can cause temporary or permanent decline, these are the lubrication change. (2) oxidation nitrification deterioration: engine oil under conditions of use, or because of heat, air and metal catalytic oxidation, or high-temperature lean-burncases, nitrification occurs, will produce resins and asphaltenes, coke and asphalteneformation . The formation of coke or sludge, resulting in further parts of the corrosion,ring sticking, plug filters. (3) additive consumption and degradation: the combustion and oxidation will consume the acid detergent, high temperature decomposition and oxidation ofsediments will be loss additives, antiwear additives and dispersants, making loss ofthe internal combustion engine lubricant protection. (4) the accumulation of contaminants: dust and sand on the road, wear metalparticles can be abrasive to the parts; fleeing into the combustion products, will accelerate the rust, corrosion and sludge generation; not burning oil through thepiston rings into the crank box, will reduce the oil viscosity, additive performanceimpact, destruction of oil film strength, resulting in increased wear and tear; coolantleak caused damage more severe than even the fuel dilution. The series TYA vacuum Lubricating oil purifier machine is used to claim and clean various high-precision lubricating oil such as hydraulic oil, mechanical oil, coolant oil, gear oil, heat treatment oil, turbine oil and so on. Feature: 1.The machine adopted deeply and precisely FH rectangular filtering system and highly polymeric adsorbing material filters. So the machine has strong ability to remove the impurity, which can filter the dirt particle completely. 2. We adopt the high quality filter material, which has a good function in anti-corrosive, thermostable, mechanical strength. Especially, the precision of eliminates impurities is high and the service life is long. Also, it has a large volume for storing the impurities. 3. The combination of coalescing separation filters and a vacuum dewater system which dewatering effectively and thoroughly. 4. The unique degas and dewater technology: Using the stereo-evaporation technical, which can separate the water and gas from the oil quickly by the multi-level water-oil separation technology. It can remove the free and dissolved water from the oil thoroughly. 5. It has the back flush system, which can clear impurities automatically. 6. Strong capability of breaking emulsification. 7. Advanced dielectric condensation device 8. This machine installs the new pressure protector, which can control the temperature automatically; also it can drain water on line by the water-separator device. So it is easy to control this machine. 9. The all electric motor is anti-explosion. The explosion proof grade is DIIBT4. 10. Adopt double-infrared fluid level auto-control systems which can control the oil inlet and the oil outlet automatically. 11. Adopt a trinity of the interlocked preventive device. Advantage:This oil purification can fast Degas, dewater, and remove the impurity and the volatile matter (for example ethyl alcohol, gasoline, ammonia and so on). Enhances the oil quality, restores the lubricating oil viscosity, augments the flash point and improves the operational performance. Guaranteed the hydraulic system and the dynamic system, the lubrication system normal operation, so the machine is set for many lines, such as the mine, metallurgy, electric power, transportation, manufacture and so on. http://oilfiltrationman.weebly.com/tya.htmlFind more oil filtration, oil filtersoil ,purification, oil treatment, oil purifier, oil recycling
The principal purpose of vacuum dehydration and purification can be to reduce free, emulsified, and dissolved water from oil, too as reliable particulate contamination. The secondary purpose of the method is te extraction of air, gases, and lumination hydrocarbon contamination in the oil. These functions are achieved utilizing the principles of minimal temperature vacuum distillation and micronic filtration Vacuum Dehydration - numerous are mindful that vacuum dehydration will remove free, emulsified and dissolved water from their lubricants. In numerous cases, high high quality vacuum dehydration units can acquire basic water content as minimal as twenty components per million. However, vacuum dehydrators also serve other functions. High high quality vacuum dehydrators are equipped with high efficiency filters that can acquire particle counts as minimal as ISO 14/12/9. In addition, refrigerants, solvents and fuels are removed by vacuum dehydration. High-Vacuum Transformer Oil Filtration And Dehydration Plants are suitable for all types of electrical insulating oils. We have standard high-vacuum filtration and dehydration plants to remove moisture (free as well as dissolved), gases, dirt and oxidation products from mineral-based and synthetic, silicon oils and others. Systems are in flow rates from 300 LPH to 12000 LPH. In order to acquire optimal dielectric strength and insulating efficiency inside of transformers and circuit breakers, dielectric oils should be kept absolutely clean up and dry. ZHONGNENG designs and builds the most effective, durable, and easily operation high vacuum transformer essential oil purification method available on the market today. Transformer essential oil remedy plant means?Old transformer essential oil is generally mixed with gas, water and contaminants, and also the new transformer essential oil sometimes, the content of the contaminants generally raises fast by time. So the transformer essential oil remedy machines can remove these associated gases, water and contaminants, and separate them in the essential oil and consider them away. After treating the essential oil by our essential oil remedy plant, the stabilized essential oil is then again ready to become used in energy transformers. Custom built plants can be provided as per customer’s specific requirement, such as more flow-rates. These plants work on low temperature, high vacuum principle. Plants mainly consist of heating, filtration and vacuum system. Heating system aids to the filtration and moisture removal. Filtration systems remove suspended particles down to 1 micron such as rust, dirt, scales, colloidal carbon etc. Vacuum Systems remove moisture (emulsified as well as dissolved) down to < 5 – 10 ppm depending on the working vacuum of the plant. Technology and benefits of the model: 1: It is for treating a range of insulating oil, including transformer oil, mutual inductor oil, change oil. 2: It is extensively applied in large scale manufacturing factory, energy station and other related industrial fields which will use transformers, specifically for more than 110 KV transformers. 3: Double point vacuum system, adopt international remarkable duplex stereo-evaparation technology and british G technology to eliminate the trace water in insulation essential oil and recover its breakdown voltage greatly. 4: Adopt Germany's 3 UG phase replay, will make the machine functioning efficaciously and safely at any situations, such as energy off, lack of phase, wrong phase position, etc. 5: Equipped with remarkable dielectric condensation devices for greatly prolong the essential oil purifier provider life. 6: A trinity of interlocked preventive unit is applied for avoid the machine becoming damanged from any incident automatically. 7: It also can be used becoming a separate vacuum method for dehydrating essential oil only, don't should operate all procedure and can save time and consumption for different ask on essential oil filtration. 8: it may purpose onsite using the transformer operating together. 9: A PLC method can be attached as per customer's requirement. 10: it may be moved easily with equipped steel wheels, it also can be created for different structure of completely enclosed type and completely enclosed trailer type to the objective of ourdoor use and indoor use. 11. a range of coloring of the model can be produced just as customer's favor. Plants are available in different types of constructions such as open & enclosed models, stationery, portable & mobile models, with single & double stage degassing / dehydration system. =================================== Contact: Mr. VienZhang [email protected][email protected]skype: vien_zhang Tel : 86 13512396086 Fax: 86 23 86197078 Chongqing Zhongneng Oil Purifier Manufacture Co.,Ltd 13 Huoju Street, Jiulong Industrial Park, Jiulongpo District, Chongqing City. China Find more on http://oilfiltrationman.weebly.com http://pureyouroil.diytrade.com http://www.zhongnengcq.cn Find more oil filtration, oil filtersoil ,purification, oil treatment, oil purifier, oil recycling
1. Oil temperature controlWorking oil temperature is 35 ~ 55 ℃, up to 70 ℃. The adverse effects of high oil temperature: (1) decline in oil viscosity, oil film damage is damage, friction increases, causing the heating system, the implementation of components (such as hydraulic cylinder) crawling; also lead to increased leakage, significantly reduce the efficiency of the system; oil through the throttle when the characteristics will change, so that the piston velocity is unstable. (2) thermal expansion of parts caused by high oil temperature, so that the action occurred deputy campaign not working or stuck. (3) When the oil temperature is over 55 ℃, the increased oil oxidation, reducing the service life, according to tests confirmed that the oil temperature is over 55 ℃ when the temperature is increased after 9 ℃, oil life shortened by half. 2. filtration controlOil filter filtration system shall be the maximum sensitivity of the filtration component selection, respectively, in suction, pressure piping, the servo control valve of the inlet, etc., in accordance with the requirements set filtration oil filter. 3. To strengthen the on-site maintenance and management(1) Check the fluid cleanliness. When checking the cleanliness of equipment, the system should also check the oil, fuel tank and oil filters for cleanliness, and cleanliness on the establishment of hydraulic equipment, in the next three scoring system. The hydraulic system for critical equipment to be random. (2) the establishment of a hydraulic system maintenance system. Level in the development of equipment maintenance content, to increase the hydraulic unit of the specific maintenance content. (3) periodic testing of oil samples. Regularly, quantitative extraction of the oil sample, check the unit volume of the oil sample size and number of impurity particles or the weight, and for the qualitative and quantitative analysis to determine whether the oil needs to be replaced. ① Oil sampling time: oil change intervals have been provided for the hydraulic equipment, the week before in the oil of the oil being used for testing samples; the new change of oil, the cumulative work of 1000h, the response to the sample test ; large sophisticated companies in the oil hydraulic equipment used in the use of 600h, should be sampled for testing. ② taking oil samples, first of all necessary equipment to clean the oil container, and not to use dirty containers in order to ensure that data is accurate and specific method of taking oil samples are as follows: When the hydraulic system does not work (ie in the stationary state), respectively in a tank top, middle and lower samples from each of the same amount of oil, stirring after the laboratory; hydraulic system is working, you can always return pipe in the system port to take the oil sample; tests required number of oil samples, usually 300 ~ 500mL / times; according to laboratory procedures for testing of oil, oil will fill a single laboratory test results, and analysis of fluid caused by changes in physical and chemical indicators of the reasons for exclusion in advance hidden faults, and into the equipment file. 4 regular cleaning. Periodically clean the filter, filter, tank, tubing and components within the dirt. Component in the disassembly should pay attention to cleanliness, all ports will be added to the plug or plastic sheeting sealed to prevent dirt intrusion system. ( 5) drain intervals. Oil change depending on whether the extent of oil contamination, currently there are three ways to determine the oil change period: ① visual oil law. It is the experience with maintenance personnel, according to some of the oil routine visual state changes (such as oil black, stinking, into a white, etc.) to decide whether oil. ② periodic oil change method. Depending on the device where the environmental site conditions, working conditions and the use of oil drain intervals, due to be replaced. This method of hydraulic equipment is applicable to large enterprises. ③ sampling assays. Regular oil sampling for laboratory tests, determination of the necessary items (such as viscosity, acid value, moisture content, particle size and concentration as well as corrosion, etc.) and indicators, according to the actual measured value oil with the required standards of oil degradation compared to determine the Should the oil change. Sampling time: general construction machinery hydraulic system should be in the oil change the week before, key equipment (such as the TBM TBM, etc.) of the hydraulic system should be carried out once every 500h sampling was conducted, results should fill in the equipment technical file . Sampling test method for key equipment and large hydraulic equipment. Former oil tank to the main house and the old oil pipeline exhausted, and the fuel tank, filter, hoses and other clean. Oil change, pay attention to cleanliness, to prevent the invasion of the hydraulic system of stolen goods, can not be mixed and for the wrong, after testing to confirm or complement the new fuel oil has reached the prescribed performance indicators, in order to join. When fuel oil must be filtered, the filters have been fatigue damage should be replaced. Add oil to reach the oil tank standard position, fuel is: first fuel to the tank top oil standard line, starting the hydraulic pump motor, the oil supply to the system of pipes, oil tank and then filling to the standard line, and then start the motor, sorepeated, until the oil remained at less than marking up the oil. by VienZhang Find more oil filtration, oil filtersoil ,purification, oil treatment, oil purifier, oil recycling
The Steam Turbine and protective actions are based on oil as the working medium, support bearings and thrust bearings also requires a lot of oil to the lubrication and cooling. Therefore, turbine lubrication system, fuel system, control system and protection systems are closely linked together to form the turbine oil system, turbine generator sets to ensure the normal operation. The turbine oil system can be divided into two groups according to conditions. The first group is the low-pressure oil system, lubrication system including oil pipelines, electricity supply to pump hydraulic oil pipe coupling and hydrogen-cooled generator seal oil pipeline system, the general system of hydraulic oil does not exceed 0.3MPa. The conditioning system and the second group of oil pipeline protection systems. In this system, adjust the pulse to pass the oil is medium, but also the hydraulic servo of the working media, change the hydraulic system depends on the power turbine, parameters and characteristics of the unit structure. The small and medium-capacity hydraulic pump for the main steam turbine 0.49-0.98MPa, with the increase in unit volume and increased steam parameters, the hydraulic control system will be further enhanced. The pressure lubrication system with a common discharge pipe and tubing, pressure tubing-conveyed from the turbine oil to each bearing, the bearing into the bearing oil depends on the temperature of operation by installation of a dedicated entrance on the bearing washer to adjust the different specifications. The conditioning system and protection system consist of components and the corresponding adjustment of the composition of the oil pipeline, the oil pipeline into the pipeline and pulse power channels. The power equal to the main pipeline pump hydraulic oil pressure in the steam turbine normal conditions, the oil pressure is constant, only the load caused by the change transition process is an exception, this time as an instant increase in traffic, the pressure will force oil reduced. The conditioning system in the pulse hydraulic pipe with turbine load and working conditions and changes in the hydraulic system can automatically change with the adjustment can also be changed by means of manual-guided institutions. The protection system in pulse pressure in the turbine oil pipeline's normal operating condition is constant, when the protective device operation, this only changes the pulse hydraulic. The turbine oil purifier is used for treating the unqualified turbine oil, especially the seriously emulsified turbine oil. This products, which can rapidly and effectively remove the water, gas and impurities, break emulsification. It aims at turbine oil’s nature of high water content, easy emulsifiable and high impurity content, and makes the oil recover the new oil's nature. 1. Breaking emulsification thoroughly with high- molecule polymeric material. 2. Dewatering very effectively with once and for two steps dehydrating method. It can thoroughly clear away the liquid water, free water and 80% dissolved water. 3.With distinctive removing impurities technique filtering through double FH trapezoidal network and absorbing by high polymer material, this machine can make the ß3 equal or surpass 200 and make the cleanness lower grade 6(NAS1638). 4.With the trapezoidal, spiral, automatic back flushing system. 5.With the advanced dielectric condensation devices. 6.On-line oil purification can be carried out with turbine or water turbine automatically without any person. Advantage:This machine breaks emulsification thoroughly, and the oil is very difficult to emulsify again after treatment. Its dehydration volume is large and it can absorb water on line. TY series, which prevent lubrication system from damage, can effectively extend the lifetime of oil and protect turbine and other machines. Find more: turbine oil purifier, turbine oil filtration, used turbine oil recycling
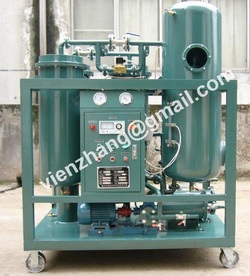 used turbine oil filtration system Applies to power plant, mill, petrochemical, mines, cement, ships, power filter oil, mineral machinery industry, turbine oils, oil, frozen oil, edible oils in hydraulic oil much moisture, gas, impurity particles ideal equipment. Features: used at home and abroad latest technology, and set gravity settlement method, and poly knot separation method, and oil-water separation method, and vacuum separation method, advantages Yu one, used imports poly knot filter material (can directly de to oil in the 80% of water), will serious emulsion oil in the of water effective decomposition, accelerated fast dehydration ability, using Germany stereo Flash steamed technology will heating of liquid oil for spray drenched film atomization processing, increases oil molecular film of area, makes dehydration effect than other filter oil machine fast 3~4 times, Additional infrared automatic energy dissipation device to effectively control the vacuum up the oil, and prevent oil from entering the vacuum pump system, using Advanced pump low noise, noise control in 70dB (a) or less. Used Sino-foreign joint venture strengthening soothing water, and oil-water separation device, further guarantee fast dehydration effect, additional automatically discharge system, in kept machine, and does not damage vacuum tank within vacuum of situation Xia automatically drainage, without artificial operation, reduced fatigue of, improve work effect, to makes filter oil machine implementation automatically online run, fine filter part using imports filter material may under customer requirements will precision control in 0.5um~3um Zhijian, makes pollution serious of oil system recovery to run turbine oil pollution of control marked system under within. Can be run independently, can also run in series on the line. Find more oil filtration, oil purification, oil treatment, oil purifier, oil recycling, oil filters
"What micron filter should be used to filter a 220 gear oil? We are looking into getting a filter cart to filter the oil while the machine is running." First, determine the optimum target cleanliness level for that specific gearbox, and the do not forget to ensure adequate breathers are fitted, as any attempts at clean-up will be lost quickly. A few tips on filter carts: First, ensure that for each type of lubricant in use, there is a dedicated filter cart to avoid cross contamination of fluids. Second, because this is fluid power generating device, ensure it complies with all the safety requirements and has a pressure venting safety valve in the event of dead-heading the pump. Third, ensure the cart includes a by-pass loop to the filters, and incorporates a sampling connector for the use of online instruments or bottle sampling. The design (pump and filter selection) of filter carts is dependent on two factors; the lubricant's viscosity grade, and the temperature at which the cart will be used. A higher viscosity, such as an ISO VG 220 oil, will require a lower flow rate in the pump to avoid high differential pressures across the filter. But this will be affected by the ambient and operating temperatures. While the use of quick connectors allow the cart to be used while the gearbox is operating (this is the optimum filtering condition), the lubricant's viscosity will also be affected by the ambient temperatures, so if this is located outdoors, assume the worst case winter temperature when looking at the viscosity issue. Of course, slowing the flow rate to avoid high differential pressures will increase the time to filter the box, and depending on the Beta ratio, the rule of thumb is to allow the volume of the gearbox to circulate seven times through the filter for effective clean-up. For example, a gearbox with 50L sump capacity and a filter cart with a 10L/min flow rate will take five minutes for one pass and approximately 35 minutes to clean up. Keep in mind the flow rate versus the time available for filtering. As to the filter rating, experience has shown a 10 micron filter capable of achieving better than ISO 17/15/12. However, if your optimum target cleanliness level is lower than this, consider a 6 micron filter. There are various ways to strike an optimum balance between flow rate and filter rating, and this includes the possibility of putting several filters in parallel to increase the flow area. As a simple guide, the differential pressure can be halved by doubling the length of the element or putting two elements in parallel. 3 micron filters will work with ISO VG 220 oils, but check the temperature conditions, and whether your target cleanliness levels require such fine filters. The cost of these elements should be considered. By Noria Find more oil filtration, oil purification, oil treatment, oil purifier, oil recycling, oil filters
a) found that vacuum degassing tank nozzle vacuum oil filter is clogged, the oil can be drained, the dry air from the oil at the entrance to purge or take othermeasures to clear. b) Vacuum Purifier before starting the vacuum pump to check the oil level and oil pollution. When oil was muddy like, let go from dirty oil discharge valve,vacuum pump oil from the pump with clean oil filling port injection, the oil levelup to the oil standard midline. c) Vacuum Purifier After each use, such as vacuum pump oil condensatecollection system has kept the oil inside, or in a vacuum degassing of the oiloverflow tank to the oil collector should be let go promptly to keep the oil, thenclose the discharge valve. d) Vacuum Purifier for every continuous operation for more than 150h, they should carefully check the vacuum system components (such as pump seal, etc.) loose. Tighten loose parts that should be good, if necessary, the limits ofthe vacuum pump should also check whether the factory standards. oil processing, oil filtering, energy saving, oil regeneration, oil processor
Vacuum oil filter is a small size, proportion, light weight, convenient, low noise, continuous long working hours, stable performance, easy to operate a new oil filter. Vacuum oil filter operation: In use before the operation, the operator should carefully read the instructions, must be familiar with the methods of operation oil filteringequipment; strict accordance with manual operation in order to operate,strict control of oil tank, to prevent the fill handle within the oil suctionpump; oil temperature control in general 40 ~ 60 ℃; regular checks ofthe oil filtering equipment used in the pipe fittings, valves for obstructions, leakage, such as find fault should immediately stop checkprocessing. Oil filter and oil system of metal pipes should take anti-staticgrounding; vacuum oil exports during the operation when the oilpressure is greater than 0.3Mpa, should check the reasons, stopcleaning or replacement when clogged filter element; operator must maintain the jobs, serious and responsible, on duty not to do otherunrelated things. Note the use of vacuum oil filter: Vacuum Oil Purifier, or other work site are strictly prohibited the use of pyrotechnics, no smoking near the oil filter equipment; duty personnel should pay attention into and out of the oil and motor functioning.Non-phase operation, 2.9 with oil heater, the pump should be open, butvoted with the heater, when the operation shut down in reverse order; if you vote with the heater should be shut down five minutes before theheater is disabled, to prevent dry burning heater accident; after work,cut power, clean up the site Find more oil filtration, oil purification, oil treatment, oil purifier, oil recycling
- When selecting filtration for high-viscosity gear oils, you should first determine the optimum target cleanliness level for that specific gearbox and ensure adequate breathers are fitted, as any attempts at cleaning the oil will be lost quickly.
- Ensure that for each type of lubricant in use, there is a dedicated filter cart to avoid cross contamination of fluids.
- Because filter carts are fluid power-generating devices, ensure they comply with all the safety requirements and have pressure venting safety valves in the event of dead-heading the pump.
- Ensure the carts include a by-pass loop to the filters, and incorporate a sampling connector for the use of online instruments or bottle sampling.
- The design (pump and filter selection) of filter carts is dependent on two factors; the lubricant's viscosity grade, and the temperature at which the cart will be used. A higher viscosity, such as an ISO VG 220 oil, will require a lower flow rate in the pump to avoid high differential pressures across the filter. But this will be affected by the ambient and operating temperatures.
- While the use of quick connectors allow the cart to be used while the gearbox is operating (this is the optimum filtering condition), the lubricant's viscosity will also be affected by the ambient temperatures. So if the gearbox is located outdoors, assume the worst case winter temperature when dealing with the viscosity issue.
- Of course, slowing the flow rate to avoid high differential pressures will increase the time to filter the gearbox, and depending on the Beta ratio of the filter, the rule of thumb is to allow the volume of the gearbox to circulate seven times through the filter for effective cleanup. For example, a gearbox with 50L sump capacity and a filter cart with a 10L/min flow rate will take five minutes for one pass and approximately 35 minutes to clean up. Keep in mind the flow rate versus the time available for filtering.
- In regards to filter rating, experience has shown that a 10 micron filter is capable of achieving better than ISO 17/15/12 oil cleanliness level. However, if your optimum target cleanliness level is lower than this, consider a 6 micron filter. There are various ways to strike an optimum balance between flow rate and filter rating, and this includes the possibility of putting several filters in parallel to increase the flow area.
- As a simple guide, the differential pressure can be halved by doubling the length of the element or putting two elements in parallel. 3 micron filters will work with ISO VG 220 oils, but check the temperature conditions, and whether your target cleanliness levels requires such fine filters. The cost of these elements should be considered.
- Electrical power considerations include the use of single or three phase, and the availability of power sockets near to the equipment, as well as ensuring that the unit is intrinsically safe for use in potentially explosive areas.
- Finally, consider using water-absorbing elements if the gearbox suffers from free and emulsified water, in addition to the use of desiccant breathers.
|